Applications
Application Factors:
The selection of contact materials for a given application should involve CTI as early in the design process as possible. CTI can help avoid expensive redesign issues by recommending proven standard contact materials and geometries or by customizing a base material for a specific application.
For example, choosing a 50% silver – 50% tungsten contact material is only part of the selection process. CTI produces three primary versions of this material. From these primary material selections, CTI further customizes the material to specific customer application requirements.
For each application, the following general guidelines in material selection and contact design should be considered:
Contact Resistance is the resistance across a pair of closed contacts which is in series with the load of the device. High contact resistance in a device can result in nuisance tripping, overheating, and even welding of the contacts. In order to avoid this problem, CTI engineers may recommend any of the following solutions:
- Increase the percent of silver and copper in the contact material
- Add or increase a silver or copper-rich surface
- Modify the refractory particle size distribution
- Change the refractory metal
- Include an adjunctive to the base material
- Change the processing parameters affecting density, hardness and/or conductivity
Contact Erosion is the loss of material due to electrical or mechanical conditions experienced at the contact-operating surface during the operation of the device. Excessive contact erosion is detrimental to the performance of the device. After determining if the cause of the erosion is mechanical wear or electrical arcing, CTI can recommend any of the following solutions:
- Change the percent of base refractory metal in the contact
- Adjust the refractory metal particle size distribution
- Increase the mass of the contact
- Change the processing parameters affecting density, hardness, and/or conductivity
Contact Welding is the bonding of the stationary and moving contacts in a device. To correct this, CTI may recommend any of the following solutions:
- Reduce the percent of silver or copper in the contact material
- Reduce or eliminate the silver-rich layer on the contact surface
- Reduce the radius on the moving contact surface
- Change the refractory metal particle size distribution
- Change the amount and/or type of refractory metal
- Design change in the apparatus
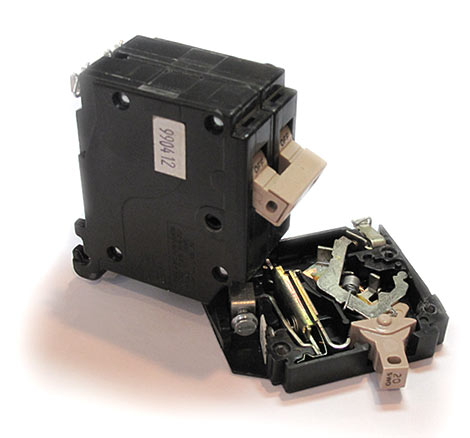
Economics of Contact Design:
Electrical contact design can be done economically in most circumstances, particularly when the contact manufacturer is involved at the front end of the design. CTI is committed to helping minimize contact cost in the early stages of design, but has also had much success in redesigning contacts to take cost out of customers' products. Listed below are suggestions to consider:
- Reduce the volume of precious metal in silver-bearing contacts by changing the composition. For example, change from 50-50 silver tungsten to 35-65 silver tungsten. Precious metal savings in the contact can easily range from 10-30%.
- Replace silver graphite with silver tungsten (or tungsten-carbide) graphite.
- Reduce contact thickness, especially on the stationary side if erosion and temperature rise are not borderline.
- Change contact shape from square to round for a reduction in material cost.
- Put a radius on all corners of a square to reduce the material cost.
- Change the face of a flat contact to one with a radius, thereby reducing material cost.
- Avoid complex geometries that require secondary machining.
- Consider outsourcing resistance, induction, torch brazing, and furnace brazing to CTI, where more efficient and more consistent brazing can be implemented.
229 West Creek Road
St. Marys, PA 15857-0149
tel: 814-834-9000 • fax: 814-834-9771
sales@contactechnologies.com